
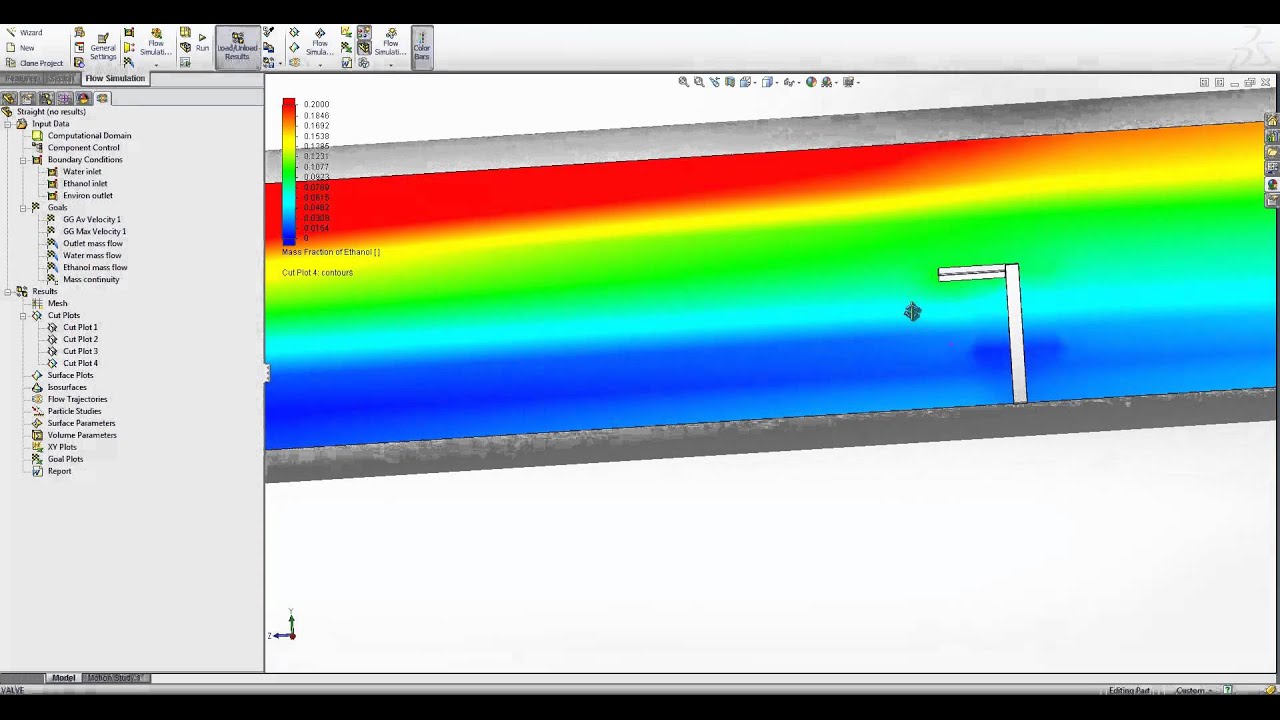
- #SOLIDWORKS FLOW SIMULATION FAN TUTORIAL ARCHIVE#
- #SOLIDWORKS FLOW SIMULATION FAN TUTORIAL SOFTWARE#
- #SOLIDWORKS FLOW SIMULATION FAN TUTORIAL FREE#
EMS and SolidWorks play a vital role in evaluating the electrical fields used with Inovio's electroporation devices, helping to determine and optimize the electrical field strength throughout the volume of space around the electrodes.If you type an equation (like 3*6) without the equals sign, then this does not create an. Create sophisticated part and assembly designs quickly and efficiently using powerful, easy. Billie Harms Junior High State Secretary Before SolidWorks entered the market, solid modeling was only available from PTC at $20,000 per seat, on.

Datum target symbols can have straight or bent leaders, but cannot be hidden (swNO_LEADER is not supported). (thrust, lift, drag, etc.) from the computed flowfield.All around leader solidworks. Post-Processing involves extracting the desired flow properties
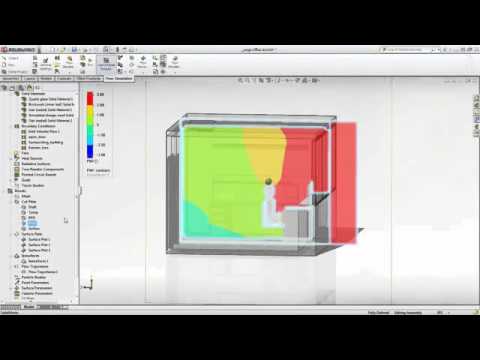
The resolution of boundary layers requires the grid to be clustered Should be consistent with the desired resolution of important features. Grid quality as defined by measures of orthogonality (especially at theīoundaries), relative grid spacing (15% to 20% stretching is consideredĪ maximum value), grid skewness, etc. Grids however, the grid blocks may be abbuting, contiguous, Currently all cases involve multi-block, structured Involves defining the structure and topology and then generating a grid The flow domain is discretized into a grid. The simulation generally starts fromĪn initial solution and uses an iterative method to reach a final flow field Since a finite flow domain is specified, physical conditions are required Structure and topology of the grid generation. Thus, the modeling often takes into account the The geometry andįlow domain are modeled in such a manner as to provide input for the
#SOLIDWORKS FLOW SIMULATION FAN TUTORIAL FREE#
Other surfacesĪre free boundaries over which flow enters or leaves. Portions of the boundary of the flowĭomain conicide with the surfaces of the body geometry. Concurrently,ĭecisions are made as to the extent of the finite flow domain in which

Required to allow an analysis with reasonable effort. Approximations of the geometry and simplifications may be
#SOLIDWORKS FLOW SIMULATION FAN TUTORIAL SOFTWARE#
This generally involves modeling the geometry with a CAD software The body about which flow is to be analyzed requires modeling.
#SOLIDWORKS FLOW SIMULATION FAN TUTORIAL ARCHIVE#
CFD Analysis Process V&V Home Archive Tutorial CFD Analysis Process
